APQP (Advanced Product Quality Planning) faser, eksempel
APQP (Avansert produktkvalitet planlegging), å være på spansk "Advanced Product Quality Planning", er det et rammeverk av prosedyrer og teknikker som brukes til å utvikle produkter i bransjen, spesielt bilindustrien..
Komplekse produkter og forsyningskjeder gir mange muligheter for feil, spesielt når nye produkter lanseres. APQP er en strukturert prosess for utforming av produkter og prosesser, med sikte på å sikre kundetilfredshet med nye produkter eller prosesser.
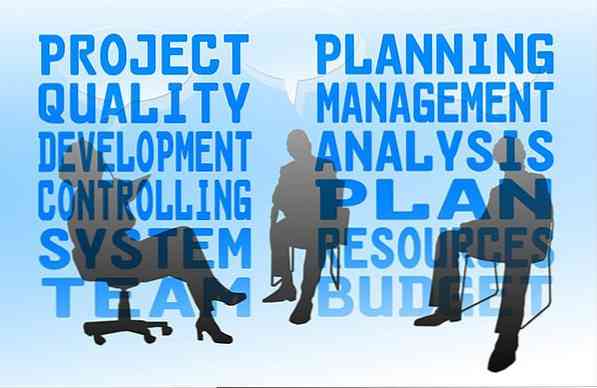
Denne tilnærmingen bruker verktøy og metoder for å redusere risikoen forbundet med endringer i et nytt produkt eller en prosess.
Formålet er å produsere en standardisert produktkvalitetskrav som tillater leverandører å designe et produkt eller en tjeneste som tilfredsstiller kunden, forenkler kommunikasjon og samarbeid mellom ulike aktiviteter.
I APQP-prosessen brukes et multifunksjonelt team som involverer markedsføring, produktdesign, innkjøp, produksjon og distribusjon. Denne prosessen brukes av General Motors, Ford, Chrysler, og dets leverandører, for produktutviklingssystemet.
index
- 1 fase
- 1.1 Fase 1: Planlegging og definisjon av programmet
- 1.2 Fase 2: Design og utvikling av produktet
- 1.3 Fase 3: Design og utvikling av produksjonsprosessen
- 1.4 Fase 4: Prosess og produkt validering
- 1.5 Fase 5: Lansering, evalueringer og kontinuerlig forbedring
- 2 Eksempel
- 2.1 Hvor å innlemme APQP
- 2.2 Bransjer som bruker den
- 3 referanser
fasene
APQP fungerer som en veileder i utviklingsprosessen og også som en standard måte å dele resultater mellom leverandører og bilforetak. Den består av fem faser:
Fase 1: Planlegging og definisjon av programmet
Når etterspørselen fra kundene krever innføring av et nytt produkt eller revisjon av en eksisterende, blir planleggingen et sentralt tema, selv før diskusjonene om design eller redesign av produktet.
I denne fasen søker planleggingen å forstå kundens behov og forventningene til produktet.
Planleggingsaktiviteter inkluderer å samle de nødvendige dataene for å definere hva kunden ønsker og deretter bruke denne informasjonen for å diskutere egenskapene til produktet.
Deretter kan du definere kvalitetsprogrammet som er nødvendig for å opprette produktet som angitt.
Resultatet av dette arbeidet er produktdesign, pålitelighet og kvalitetsmål.
Fase 2: Produktdesign og utvikling
Formålet med denne fasen er å fullføre produktdesignet. Dette er også hvor en evaluering av produktets levedyktighet kommer inn i spill. Resultatene fra arbeid i denne fasen inkluderer:
- Gjennomgå og verifisere fullført design.
- Definerte spesifikasjoner for materialer og utstyrskrav.
- Analyse av effekt og feilmodus for det ferdige designet for å evaluere feilfeilene.
- Kontrollplaner etablert for opprettelsen av produktprototypen.
Fase 3: Design og utvikling av produksjonsprosessen
Denne fasen fokuserer på planlegging av produksjonsprosessen som vil produsere det nye eller forbedrede produktet.
Målet er å designe og utvikle produksjonsprosessen med hensyn til produktets spesifikasjoner og kvalitet og produksjonskostnadene.
Prosessen må være i stand til å produsere nødvendige mengder for å tilfredsstille forbrukernes forventede etterspørsel, samtidig som effektiviteten opprettholdes. Resultatene i denne fasen inkluderer:
- En komplett konfigurasjon av prosessflyten.
- En analyse av effekt og feilmodus av hele prosessen for å identifisere og håndtere risikoen.
- Kvalitetsspesifikasjoner for driftsprosessen.
- Emballasje og etterbehandlingskrav til produktet.
Fase 4: Prosess og produkt validering
Dette er testfasen for å validere produksjonsprosessen og sluttproduktet. Trinnene i denne fasen inkluderer:
- Bekreftelse av kapasiteten og påliteligheten til produksjonsprosessen. På samme måte av kriteriet for aksept av kvaliteten på produktet.
- Realisering av testproduksjonsløp.
- Produkttest for å bekrefte effektiviteten av produksjonsmetoden som ble implementert.
- Gjør nødvendige justeringer før du går videre til neste fase.
Fase 5: Lansering, evalueringer og kontinuerlig forbedring
I denne fasen oppstår lanseringen av storskala produksjon, med vekt på å evaluere og forbedre prosessene.
Blant søylene i denne fasen er reduksjon av prosessvariasjoner, identifisering av problemer, samt igangsetting av korrigerende tiltak for å støtte kontinuerlig forbedring.
Det er også innsamling og evaluering av tilbakemeldinger fra kunder og data relatert til prosess effektivitet og kvalitetsplanlegging. Resultatene inkluderer:
- En bedre produksjonsprosess, ved å redusere prosessvariasjonene.
- Forbedring av kvaliteten i leveransen av produktet og tjenesten til kunden.
- Forbedring i kundetilfredshet.
eksempel
Hvor å innlemme APQP
- Utvikling av krav fra klientens stemme, ved hjelp av implementeringen av kvalitetsfunksjonen.
- Utvikling av en produktkvalitetsplan integrert i prosjektplanen.
- Produktdesign aktiviteter som kommuniserer spesielle egenskaper eller nøkler til prosessdesignaktiviteten, før design slippes ut. Dette inkluderer nye former og deler, strammere toleranser og nye materialer.
- Utvikling av testplaner.
- Bruk av formell design gjennomgang for å spore fremgang.
- Planlegging, oppkjøp og installasjon av tilstrekkelig utstyr og verktøy av prosessen, i henhold til design toleranser gitt av kilden til produktdesign.
- Kommunikasjon av forslag fra montasje- og produksjonspersonell på måter å bedre montere et produkt på.
- Etablering av tilstrekkelige kvalitetskontroller for spesielle egenskaper eller nøkler til et produkt eller parametere av en prosess, som fortsatt utgjør risikoen for potensielle feil.
- Realisering av studier av stabilitet og kapasitet av spesielle egenskaper for å forstå dagens variasjon og dermed forutsi fremtidig ytelse med statistisk kontroll av prosesser og prosessens kapasitet.
Bransjer som bruker den
Ford Motor Company publiserte den første avanserte kvalitetsplanleggingsmanualen for sine leverandører i begynnelsen av 1980-tallet. Dette hjalp Ford-leverandører til å utvikle hensiktsmessige forebyggings- og detekteringskontroller for nye produkter, og dermed støtte bedriftens kvalitetsarbeid.
På slutten av 80-tallet brukte de viktigste produsentene av bilindustrien APQP-programmene. General Motors, Ford og Chrysler hadde det implementert og så da behovet for å forene for å skape for sine leverandører en felles kjerne av produktkvalitet planlegging prinsipper.
Retningslinjene ble etablert tidlig på 1990-tallet for å sikre at APQP-protokollene ble fulgt i et standardisert format.
Representantene til de tre bilprodusentene og American Society for Quality Control opprettet en gruppe kvalitetskrav for å få en felles forståelse av temaer av felles interesse innen bilindustrien..
Denne metoden brukes nå også av progressive selskaper for å garantere kvalitet og ytelse gjennom planlegging.
referanser
- Wikipedia, den frie encyklopedi (2018). Avansert produktkvalitet planlegging. Hentet fra: en.wikipedia.org.
- NPD Solutions (2018). Avansert produktkvalitet planlegging. Hentet fra: npd-solutions.com.
- Quality-One (2018). Avansert produktkvalitetsplanlegging (APQP). Hentet fra: quality-one.com.
- Baits (2018). De fem faser av APQP: En oversikt over nøkkelkrav. Hentet fra: cebos.com.
- David Ingram (2018). Avansert produktkvalitet planlegging. Small Business - Chron.com. Tatt fra: smallbusiness.chron.com.